Was ist PROFINET?
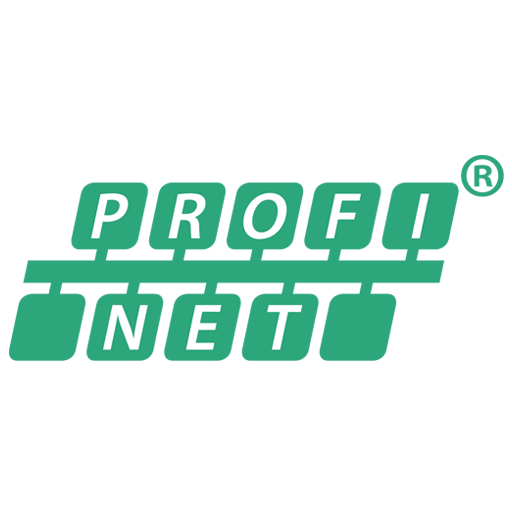
PROFINET is an open Industrial Ethernet standard. It is intended for industrial applications such as manufacturing and process automation and enables data communication with deterministic cycle times. The standard has a modular structure, supports various transmission media and uses TCP/IP. It defines four conformity classes for the different functions and requirements for real-time communication.
PROFINET stands for Process Field Network. It is an open standard for industrial Ethernet from Profibus & Profinet International (PI) and the PROFIBUS User Organization eV (PNO). The standard is the successor to PROFIBUS and is specified in the IEC standards IEC 61158 and IEC 61784.
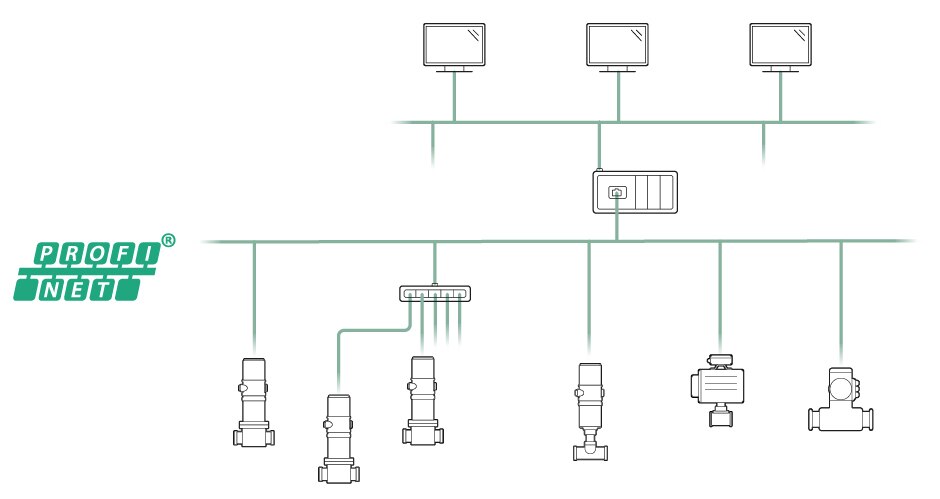
How does PROFINET work?
The communication concept is modular, enables real-time data exchange and allows the integration of various fieldbus systems such as PROFIBUS, DeviceNet or Interbus. Technically, Process Field Network is based on Ethernet and TCP/IP. Various transmission media are supported.
Basic functionality and properties
Based on Fast Ethernet, various network topologies such as line, star, ring and tree topologies can be implemented. PROFINET I/O defines data communication and follows the provider-consumer model. The model recognizes three different device types: the IO device, IO controller and IO supervisor.
An IO device is a decentralized field device that is connected to one or more IO controllers via PROFINET IO. It is controlled and monitored by the IO controller. IO devices can be parameterized and diagnosed using an IO supervisor. An IO system requires at least one IO controller and one or more IO devices.
In principle, any automation device with an Ethernet interface can be an IO controller and IO device at the same time. The IO supervisor is optional and often only integrated temporarily. The IO system described can be used to exchange process data in real time.
Advantages of Process Field Network PROFINET
- modular range of functions
- based on proven Ethernet technology and TCP/IP
- supports different wired and wireless transmission media
- different network topologies can be mapped
- enables real-time communication with short, deterministic bus cycle times
- various existing fieldbus systems such as PROFIBUS, DeviceNet and Interbus can be integrated
- can be used for various applications in manufacturing and process automation
- easily expandable
- integrated diagnostic functions
- integrated security features
- automated redundancy – high availability and operational reliability
- integrated functions to optimize energy efficiency
- globally accepted standard
- Interoperability and connectivity of devices from different manufacturers
- continuous development of the standard